Effective HoS Planning: Staying Compliant and Ahead of Schedule
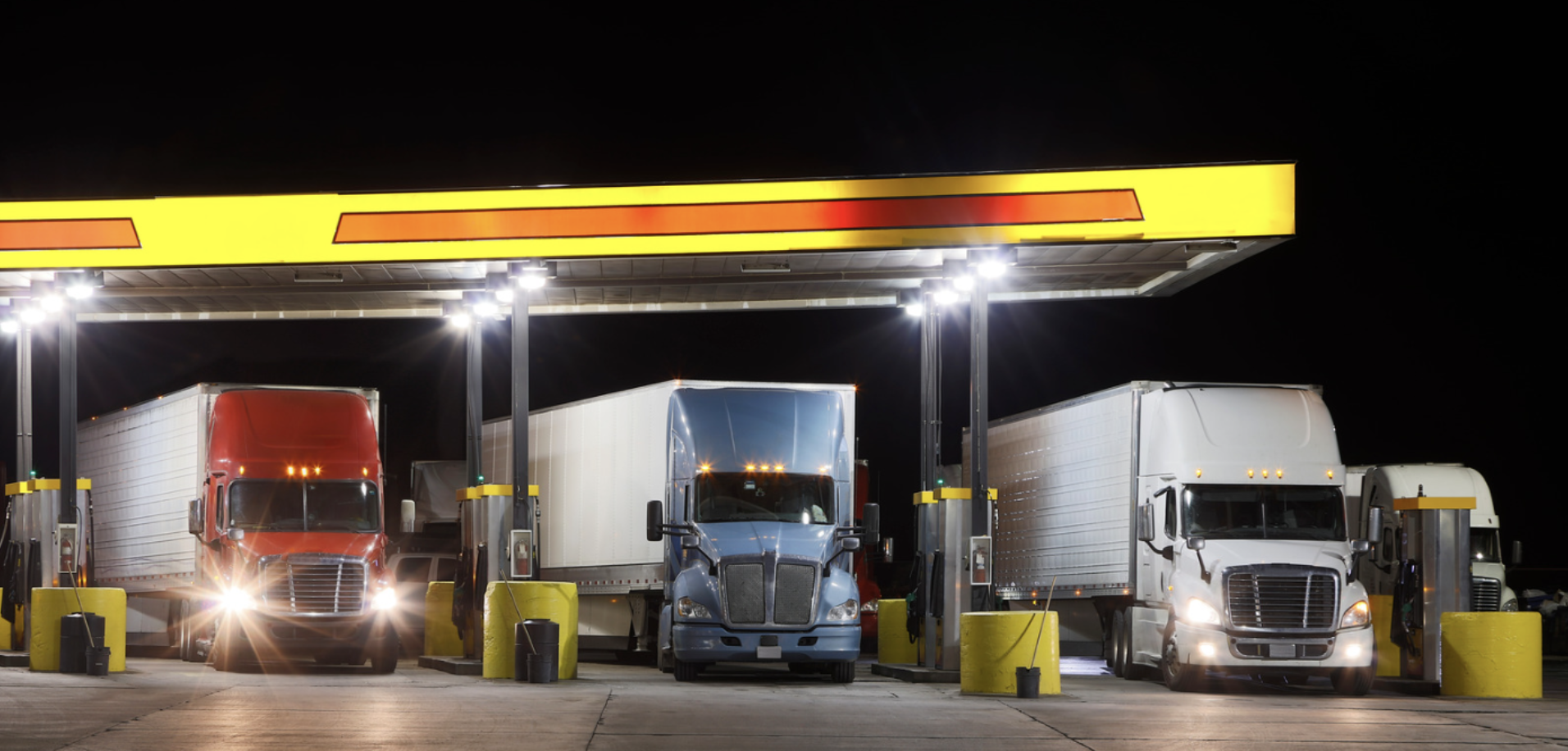
Introduction
Adhering to the regulations set by the Federal Motor Carrier Safety Administration (FMCSA) for Hours of Service (HoS) is crucial for truck drivers, as it helps prevent driver fatigue and ensures road safety. This blog will explore practical strategies for HoS planning.
Key HoS Regulations
Under the Hours of Service (HoS) rules, drivers are restricted from driving for more than 11 hours within a 14-hour on-duty period. They must also adhere to weekly limits of 60 hours on duty in 7 days or 70 hours in 8 days. In addition to these basic rules, the regulations include mandatory breaks, specific periods between shifts, provisions for a sleeper berth, and the 34-hour restart rule. These added regulations can make compliance more complicated.
Consequences of Non-Compliance
Failure to comply with the HoS regulations can lead to significant consequences, including hefty fines ranging from $1,000 to $16,000 per violation for drivers and Carriers. Moreover, the FMCSA can suspend licenses and publicize negative safety scores, affecting a driver's job prospects and a Carrier's ability to secure loads.
Effective trip planning and utilizing "Recap hours" can assist Carriers and drivers in optimizing their operations while ensuring full compliance with the HoS regulations. Let's explore strategies for efficient HoS planning, emphasizing the importance of electronic logging devices (ELDs) and other tools while explaining how Recap hours can help avoid the need for a 34-hour restart when necessary.
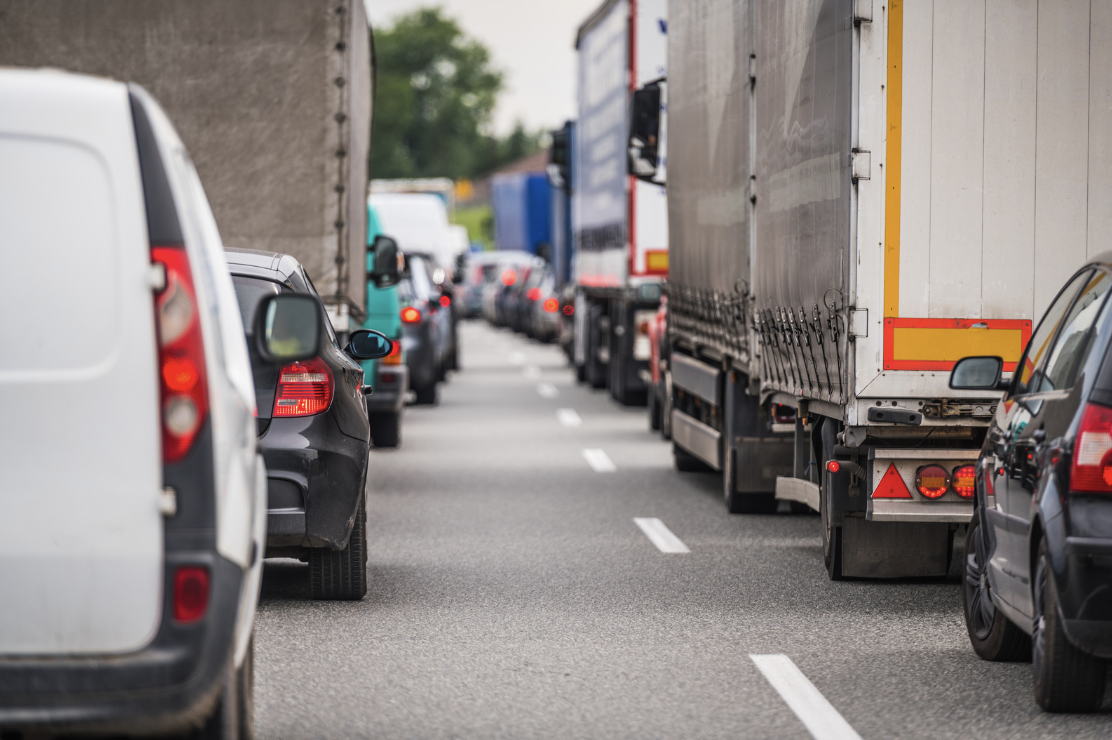
The Operational Challenges of HoS Compliance
One of the significant challenges in the trucking industry is the unpredictability of events that can disrupt schedules, such as breakdowns, adverse weather conditions, and extended waiting times at destinations—factors often beyond the Carrier's control. These disruptions can cause a chain reaction to staying compliant with the HoS regulations.
If a driver encounters substantial delays and reaches their 11-hour driving limit within a 14-hour on-duty period, they must stop and take a mandatory 10-hour break before resuming their journey. Furthermore, suppose the same driver has been maximizing their daily hours over multiple consecutive days. In that case, they may also be required to take a 34-hour restart if they exceed the 60-hour on-duty limit within a 7-day consecutive period or 70 hours over 8 days. After a 34-hour restart, the driver’s available hours are fully replenished.
Risks and Challenges in Long Haul
Unfortunately, some drivers put themselves, the public, and their own Carrier safety rating at risk by exceeding speed limits or violating HoS allowances to compensate for delays. Errors in calculating schedules, ETAs, or excessive waiting time at pickup will increase the chances of delayed delivery, especially on long-haul routes. Carriers find themselves in a precarious position, as late deliveries can impact their on-time delivery scores, leading to lower customer satisfaction and potential loss of business.
Diligent dispatchers should be well-prepared for such scenarios and proactively predict potential issues to avoid maximizing a driver's hours in situations where timely delivery may not be feasible. However, estimating accurate ETAs is manual for most Carriers and requires support staff to monitor multiple software interfaces, perform tedious calculations, and regularly check in with the driver on duty to get their input.
Furthermore, Dispatchers must carry out manual ETA calculations regularly to stay accurate. When a broker or shipper inquires about the status, someone repeats the calculation to provide the most up-to-date information. For large fleets handling hundreds or thousands of loads per month, this process becomes increasingly burdensome and almost impossible to track accurately for every load, leading to unpredictable delays and potential compliance violations.
While electronic logging devices (ELDs) provide valuable insights into remaining driving and on-duty hours, they do not account for real-world driving conditions, travel times, and appointment schedules. Drivers and dispatchers are often left to perform their calculations to predict on-time delivery, leading to risky behaviors like skipping breaks, speeding, or exceeding allocated HoS limits for the day.
For long-haul fleets, drivers often run on the Recap schedule; a miscalculation or excessive delay could force a mandatory 34-hour break, which could require a relay driver to finish the load if one is available. The process becomes cumbersome and error-prone for fleets handling hundreds or thousands of monthly loads. It requires diligent tracking and tracing throughout each load's journey, ultimately highlighting the need for more efficient and automated solutions. Thankfully, with the advent of artificial intelligence and machine learning, tools like Channel19 can automate this manual work with higher accuracy than human calculations and provide accurate real-time alerts, removing the burden from the Dispatch support team.
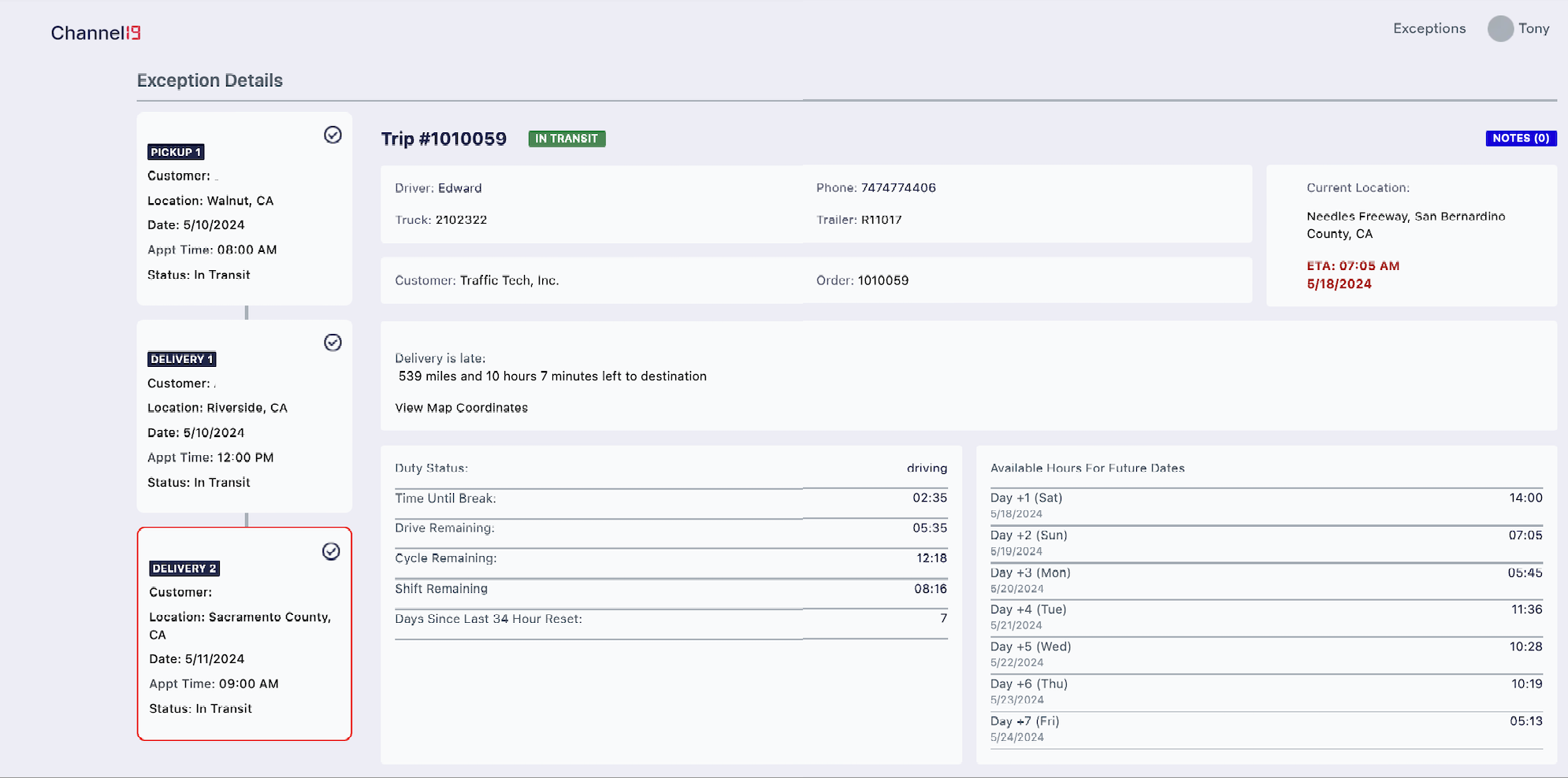
Beyond the ELD and TMS
Transportation management systems (TMS) and electronic logging devices (ELDs) we’ve encountered at Channel19 do not provide dispatchers with accurate, up-to-date estimated time of arrivals (ETAs) based on real-world conditions, appointment times, and future HoS. Drivers and dispatchers must carefully balance many factors, including load times, traffic patterns, speed limits, vehicle capabilities, and the driver's physical and mental fatigue, to schedule, dispatch, and manage loads.
With a 14-hour on-duty clock that starts at the beginning of the day and keeps rolling regardless of circumstances, the wasted time cuts into available drive time, leading to loads sitting idle instead of advancing and drivers sleeping in their trucks instead of getting home on time.
Recap hours allow drivers to operate for as many days as they like, provided they stay within 60 hours on duty within 7 days. After the 7th day, the driver can reclaim the hours driven on the previous 7th day as a drivable allowance, essentially rolling over the hours. While this schedule allows trucks, drivers, and loads to remain in transit for longer periods without requiring a 34-hour reset, a miscalculation could result in a driver exceeding their allowance and immediately being forced to take a 34-hour rest break.
Some modern ELDs account for recap scenarios but often fail to predict beyond the following day, leaving a significant gap in predictive capabilities. This is where tools like Channel19 come into play. Channel19 handles these complex and error-prone workflows by integrating with Carriers' existing systems. Predictive AI software considers appointment times, location data, traffic conditions, and past and future HoS to provide Carriers with accurate ETAs and alerts if a delay is likely to occur, allowing them to take proactive measures.
For example, in long-haul trips spanning multiple days, Channel19 considers a driver's hours for upcoming days and previous days' hours if operating on a recap schedule, ensuring that the driver has enough available hours to make the appointment time. This lets dispatchers provide shippers with ample warning of potential delays, boosting trust and satisfaction.
If you'd like to learn more about Channel19's exception management tools and how they can streamline your operations while ensuring compliance, please contact us for a demo.